The buyer requested a third-party Final Random Inspection (FRI) to ensure product quality and conformity before shipment. An objective assessment from an external party mitigates the risk of defects.
Quality control is a crucial step in the manufacturing process, particularly when the buyer and seller are operating from different geographical locations. A third-party Final Random Inspection provides an impartial verification of the products, ensuring they meet the agreed-upon standards and specifications.
This independent evaluation often serves as a final checkpoint before the buyer accepts the goods and authorizes shipment. By enlisting an unbiased inspector, buyers can protect their investment and avoid the costly implications of receiving subpar goods. Engaging in this best practice demonstrates the buyer’s commitment to quality and can help build trust between the trading parties, paving the way for successful, long-term business relationships.
:max_bytes(150000):strip_icc()/4-things-landlords-are-not-allowed-do_final-b75d9df2c42841239d7f7222cceba6c1.png)
Credit: www.investopedia.com
Introduction To Final Random Inspection
Final Random Inspection (FRI) is a crucial step for quality control. It is a product assessment done before items are shipped to a buyer. The buyer wants to make sure the products meet their standards. They do not want any bad surprises. So, they ask for a third party to check the goods. The third party is not from the buyer or the seller. This means they are neutral and fair. Their job is to look at the items randomly. This is to mimic what a customer might get. They check the number, quality, packaging, and more. Their report helps the buyer decide to accept or reject the shipment.
Buyer’s Rationale For Third Party Fri
Buyers often seek third-party Final Random Inspections (FRI) to ensure that products meet their standards. A third-party FRI provides an objective assessment of quality before shipment. This is crucial for maintaining brand reputation and customer satisfaction. Independent inspectors are skilled at identifying defects and non-compliances. Their expertise helps in delivering consistent product quality. Engaging neutral parties eliminates bias, as they have no ties with the seller. This impartiality boosts buyer confidence in the inspection results. Buyers aim to shield their investments against potential risks. Reliable inspections reduce costly returns and recalls. A third-party FRI serves as a safety net, ensuring that products shipped are worth the cost. Trust in products grows when a trusted inspector verifies quality.
The Benefits Of An Independent Inspection
A Third Party Final Random Inspection (Fri) offers an unbiased product quality check. Such reviews happen before shipping the client’s goods. A third party’s viewpoint is dependable and precise, providing clear insights into the product’s condition. This step ensures that all items meet the specified standards. Buyers gain confidence with independent quality validation. It signifies that products have been thoroughly examined by experts. This neutrality can strengthen buyer-supplier relationships. Suppliers, too, can affirm their commitment to delivering high-quality items. This practice often results in fewer disputes and heightened trust between trading parties.
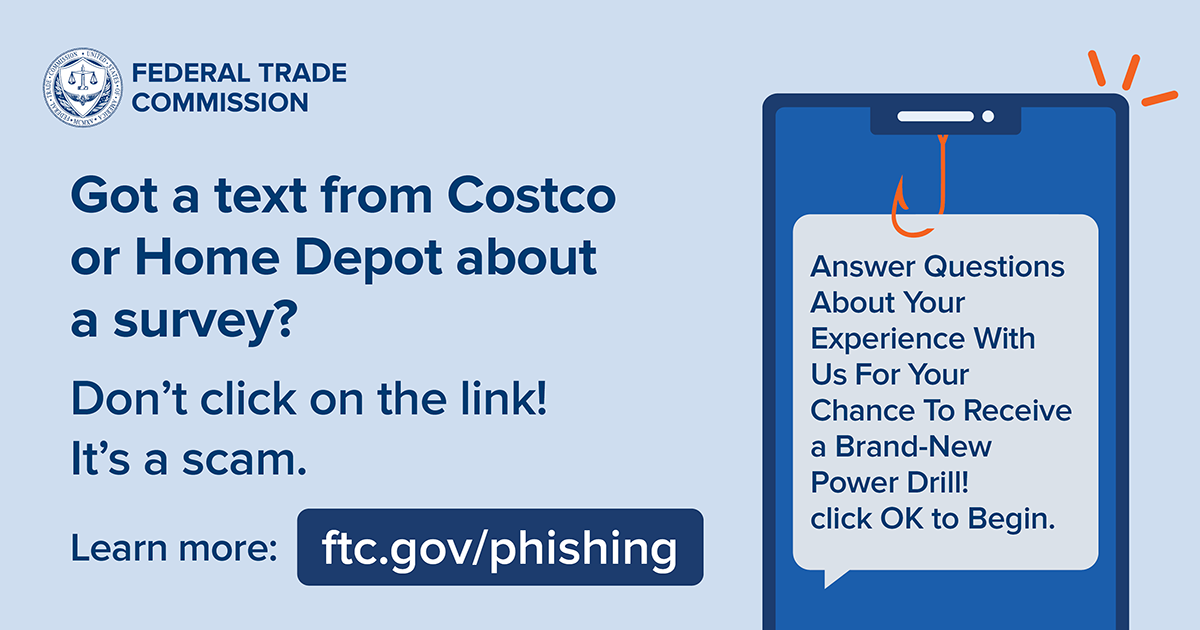
Credit: consumer.ftc.gov
The Fri Process
Understanding the FRI process involves recognizing key steps. Buyers request a Third Party Final Random Inspection (FRI) to ensure product standards before shipment. Pre-Inspection Preparations: Initial steps include verifying the shipment details. This involves checking quantities and packing. The inspection agency reviews product specifications and confirms the inspection schedule. On-site Inspection Procedures: Inspectors visit the factory on the scheduled date. They conduct a random sampling of products based on accepted quality control standards such as AQL. Inspectors perform visual and functional checks to validate quality, labeling, and packaging. The results determine if the batch meets the buyer’s requirements.
Criteria For Third Party Fri
Buyers request a Third Party Fri to ensure product quality. They want an unbiased inspection of goods before shipment. Third Party FRI sets clear quality standards. A third-party inspection defines what is good or bad. It uses specific criteria. The criteria include materials, design, and performance. These benchmarks guide the inspection process. Inspectors check against these benchmarks. They confirm if products meet buyer expectations. Setting quality benchmarks ensures consistent product quality.
Understanding The Inspection Report
Third party Final Random Inspection (FRI) serves as a crucial checkpoint. It ensures that all products meet predefined standards. Quality, quantity, and packaging are key factors. Businesses must understand the inspection report in detail.
Aspect | Compliance Requirement | Finding |
---|---|---|
Quality | Adherence to product specifications | Conformity or deviations |
Quantity | Exact match of order quantities | Shortages or excesses |
Packaging | Sturdy and correct labeling | Any damage or mislabeling |
Through clear metrics, companies can evaluate product batches. This ensures only quality goods are shipped. Failing to pass the FRI can lead to shipments being rejected. So, it’s essential for businesses to understand the finer details. Key findings guide future improvements, enhancing customer satisfaction.
Common Issues Identified During Fri
Buyers commonly request a Third Party Final Random Inspection (FRI) to check goods before shipment. Product defects can range from minor aesthetic blemishes to significant functional issues. These imperfections affect product quality and customer satisfaction. Consistency is key in manufacturing, hence, variances in size, color, or materials are red flags. Similarly, packaging and labeling errors can result in returned shipments and lost sales. Accurate labeling is crucial for meeting legal standards and informing users. Strong packaging ensures product safety during transit.
Inspection Area | Common Issues |
---|---|
Product Quality | Defects, Variances |
Packaging | Strength, Printing Errors |
Labeling | Accuracy, Compliance |
Actions Following An Unsuccessful Fri
Buyers may request a third-party Final Random Inspection (FRI) to ensure product quality and standards. After an unsuccessful FRI, it is crucial to take immediate action. Strong communication with suppliers is necessary to discuss failures and seek corrective measures. Addressing defects and quality issues quickly can help save the deal. Both parties need to agree on effective remedies. These may include product fixes, discounts, or refunds. Each situation requires a tailored solution based on the type and severity of the issues found.
The Role Of Technology In Modern Inspections
Technology revolutionizes how inspections are performed nowadays. Inspection processes are now more reliable and efficient, with digital tools at their core. Software applications assist in recording data accurately. Handheld devices streamline on-site work. Photos and reports become instantly accessible. Cloud-based platforms ensure real-time updates. This digital integration enables buyers to maintain high standards. Artificial Intelligence (AI) is shaping the future of inspections. AI-driven analysis predicts potential issues. It suggests improvements. Machine learning algorithms adapt to new inspection data. This leads to smarter, faster decision-making. Overall, AI augments third party Final Random Inspection (FRI) effectiveness.
Choosing A Reliable Inspection Partner
Selecting the right inspection partner ensures product quality. Buyers demand a third-party final random inspection (FRI) to guarantee standards. This step is crucial before shipping. A credible inspection agency must have a proven track record. Such agencies maintain quality integrity and high service standards. Valid certifications and industry experience are keys. Look for agencies with global recognition and client testimonials. Detailed reports and timely communication are essential. Choose an agency with clear procedures. They should prioritize your needs. Ensure they have a wide range of services.
Fri In Different Industries
The Final Random Inspection (FRI) serves a critical role in quality control across diverse sectors. Companies prioritize FRI to ensure the product meets the buyer’s standards. With a focus on the apparel industry, one case study demonstrated the FRI’s effectiveness in identifying stitching defects before shipment. This saved the seller from costly returns. Another industry, the electronics sector, also relies on FRI for product integrity. A report highlighted issues caught like wiring problems and battery defects. By addressing these before delivery, brand reputation remains intact. Meanwhile, in the food industry, FRIs are less common due to perishability. Yet, a case was noted where an FRI on packaging prevented a large batch of goods from spoiling. FRIs across industries are essential for quality assurance.
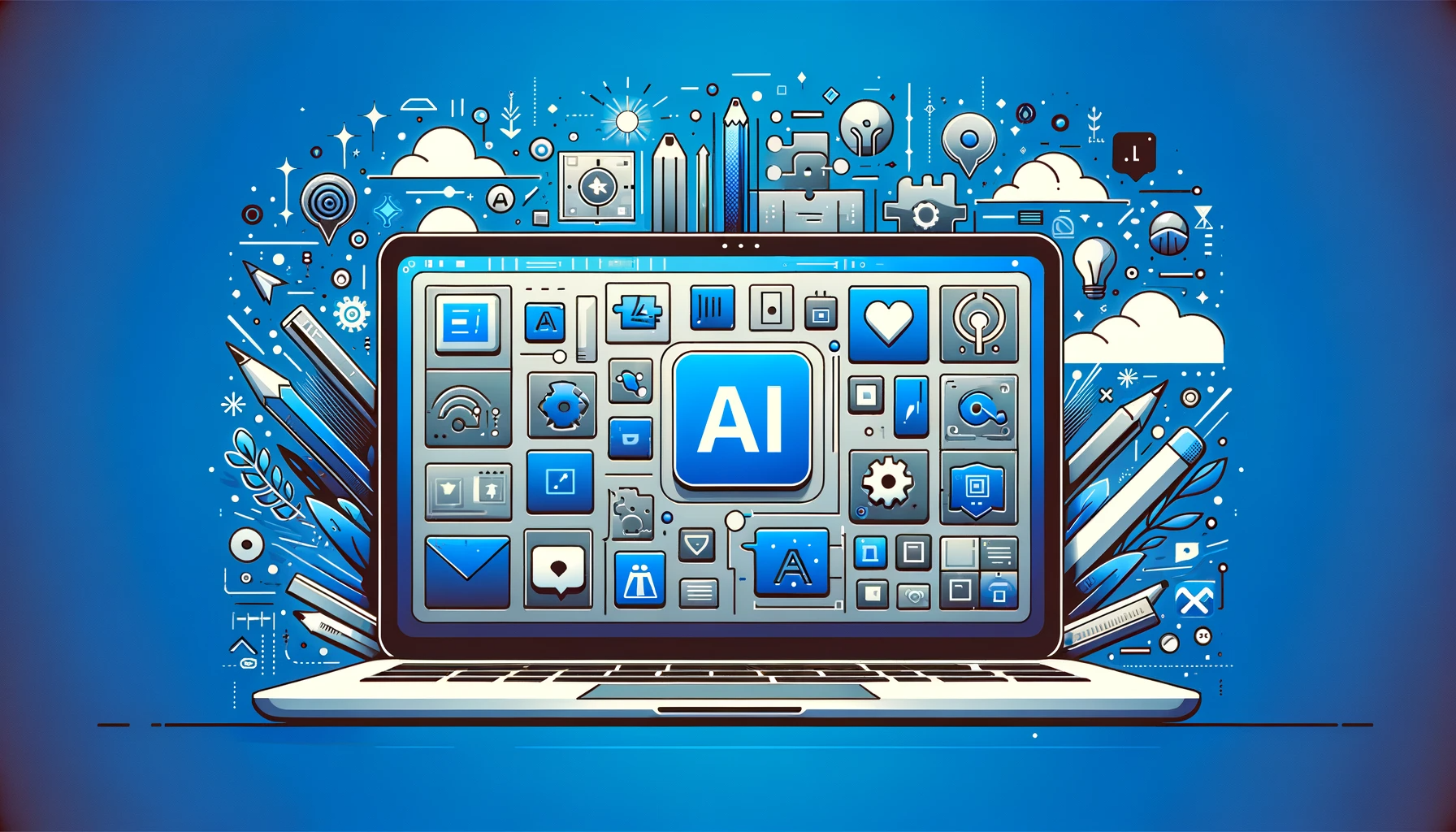
Credit: www.synthesia.io
Frequently Asked Questions For 16. Why Did The Buyer Ask For A Third Party Fri (fri- Final Random Inspection).
What Is A Third Party Fri In Purchasing?
A Third Party FRI, or Final Random Inspection, is an objective quality control process. Conducted by independent inspectors, it ensures that goods meet specific criteria before shipment. This impartial assessment helps maintain product standards and reduce defects.
Why Do Buyers Request Final Random Inspections?
Buyers request Final Random Inspections to verify product quality, specifications, and quantities. It minimizes the risk of defective items reaching the customer, ensuring that the shipment reflects the initial agreement between buyer and seller.
How Does Third Party Fri Protect Buyers?
Third Party FRI protects buyers by providing an unbiased evaluation of the products just before shipping. It detects any non-conformities early, offering a chance to rectify issues. This ensures only high-quality products are delivered to end-users.
What Takes Place During A Final Random Inspection?
During a Final Random Inspection, third-party inspectors randomly select and check items for quality, packaging, labeling, and functionality. They make sure the products comply with the purchase order, standards, and regulations before shipment.
Conclusion
Understanding the buyer’s choice for a third-party Final Random Inspection (FRI) is key. It boils down to ensuring product quality and compliance before shipment. This due diligence can save costs and safeguard brand reputation. Embrace FRI as a step towards unwavering customer satisfaction and market success.