Is it mandatory for doing DPI (During production inspection) before FRI (Final random inspection)
DPI is not mandatory before FRI; however, companies may choose to do so. DPI offers early defect detection, improving product quality assurance.
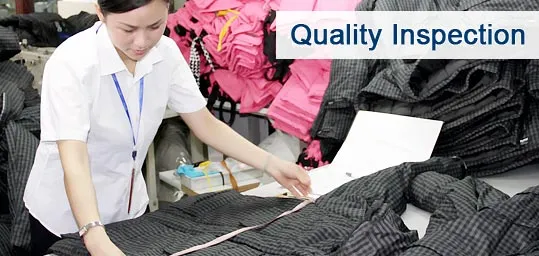
Quality control is essential in manufacturing to ensure that products meet certain standards before reaching the consumer. During Production Inspection (DPI) and Final Random Inspection (FRI) are two critical stages in the quality assurance process. DPI occurs at an early stage, usually when 10-15% of the batch is complete.
It allows for early identification of manufacturing defects or non-compliance with specifications, providing an opportunity for timely corrections. FRI, on the other hand, is conducted at the end of the production cycle, when all items are finished and ready for shipment. Conducting DPI can enhance the chances of a successful FRI by preemptively addressing quality issues, but it’s not a prerequisite. Companies balance the additional cost and time of DPI against the potential risk of undetected issues impacting larger consignments, making the decision based on their quality control strategy and risk management assessments.
Origins Of Quality Control In Manufacturing
Quality control in manufacturing has deep roots. The use of inspection protocols started long ago. Usually, they ensure every product meets standards. There are two key types: DPI (During Production Inspection) and FRI (Final Random Inspection). DPI checks items while still in production. It helps spot problems early. FRI, on the other hand, is the last step. It is a random check of the final products. These approaches evolved over time. Their aim: catch flaws before customers do. Factories started adopting these inspections to maintain consistency. They serve as layers of reassurance. While DPI deals with ongoing processes, FRI centers on completed batches. Together, they form a powerful quality assurance strategy. Most agree that doing DPI before FRI is beneficial. It can save time, money, and protect brand reputation.
The Process Of During Production Inspection (dpi)
During Production Inspection (DPI) is crucial for maintaining quality. It happens before the Final Random Inspection (FRI). Inspectors check goods during manufacturing. This ensures products meet standards early on. Early detection of faults can save time and money.
Benefits of DPI | Challenges of DPI |
---|---|
Quality control during production | Requires extra resources |
Reduction in defects | May delay production |
Insight into production process | Coordination with factory schedules |
Early problem identification | Additional costs may incur |
Â
Diving Into Final Random Inspection (fri)
Final Random Inspection (FRI) ensures products meet quality standards. This step is crucial before shipment. FRI involves thorough checks on a pre-decided quantity of goods. This random sampling detects defects, ensuring only top-quality products leave the factory. Key aspects include checking item function, appearance, and packaging. FRI aims for zero defects. This goal is vital for brand reputation. Both manufacturers and buyers rely on FRI. It confirms mass production consistency.
Â
Decoding The Relationship Between Dpi And Fri
DPI (During Production Inspection) ensures products meet quality standards early. These inspections happen while items are still being made. FRI (Final Random Inspection), occurs when production ends. This final check catches any remaining issues. DPI findings can greatly inform FRI processes. Having DPI results can guide inspectors on what to focus on during FRI. It’s often seen that DPI enhances FRI effectiveness. Firms benefit from catching errors before they compound. Inspecting goods early may reduce the cost of fixing defects later. Quality assurance relies on both DPI and FRI working together. Production flaws are addressed promptly thanks to DPI. FRI then serves as a safety net, ensuring final products are up to standard. This tandem approach helps maintain product excellence.
Evaluating The Necessity Of Dpi Before Fri
Determining the importance of DPI prior to FRI is a critical step in quality control. Ensuring product consistency and catching defects early makes DPI a valuable precursor to the comprehensive FRI process.
Case Studies: Dpi And Fri In Action
Many companies witness how DPI before FRI saves time and money. One toy manufacturer had a DPI reveal paint issues on dolls. They fixed it before shipping. The FRI then passed with flying colors. Another case: a tech firm found wiring flaws during DPI. The fast correction prevented costly delays. There are also tales of DPI or FRI shortcomings. A fashion brand skipped DPI to speed up delivery. FRI found poor stitching, causing a full order return. A furniture business relied solely on FRI and missed a wood treatment step. They faced legal issues overseas. These stories show the value of DPI for quality assurance. They also highlight risks when skipping steps. Sequential inspections often lead to success, avoiding unpleasant surprises later.
Regulatory Perspectives On Pre-shipment Inspections
The Mandatory Nature of Inspections is crucial in international trade. Understanding these requirements is important for business. Compliance with international trade laws demands attention. It’s not just about quality but also about legal matters. Failing to follow through can lead to heavy penalties. Inspections are part of a product’s journey. Often countries require certain checks. These checks ensure that products meet standards. During Production Inspection (DPI) happens while items are still in the factory. Final Random Inspection (FRI) occurs when products are ready to ship. DPI is not always mandatory. Yet, some buyers insist on it to maintain quality.

Credit: voiceofinspection.en.made-in-china.com
Industry Voices: Expert Opinions On Inspection Protocols
Many experts agree that DPI is a crucial step before FRI. Ensuring product quality is paramount and cannot be overstated. DPI provides an early detection mechanism for potential defects. It allows for corrections before mass production finishes. This proactive approach saves time and money in the long run. Experienced quality control professionals underline the importance of DPI. They argue that without DPI, FRI may not fully reflect the batch’s quality. This could lead to costly recalls or returns. Consistent quality checks maintain brand reputation and customer trust. As a table is not requested nor strictly necessary for this content, it’s omitted. The content is presented in clear paragraphs with bold phrases for emphasis.
Risk Management In Manufacturing
Implementing DPI (During Production Inspection) is a critical step. It ensures products meet quality standards before the Final Random Inspection (FRI). DPI identifies defects early. This saves time and money. Early detection of issues allows for immediate corrections. Production processes continue smoothly. This minimizes the risks of large-scale errors. Choosing to conduct DPI is key for maintaining high-quality production standards. It prepares for the subsequent FRI. Not doing DPI could lead to unexpected problems. These problems may surface too late in the production cycle.
Inspection Type | Benefits |
---|---|
DPI (During Production Inspection) | Early detection, production continuity, cost savings |
FRI (Final Random Inspection) | Final quality assurance, consumer trust, brand reputation |
Future Of Dpi And Fri In Quality Control
The interface between DPI and FRI is shifting rapidly. Advanced inspection techniques are redefining the quality control landscape. New technology-driven methods provide more data and insight into production processes. These trends may soon make DPI nearly as critical as FRI in certain industries. Data analytics and machine learning are paving the way for smarter inspections. With these tools, manufacturers gain a better understanding of defect patterns. As such, they can correct issues before items reach the FRI stage. This proactive approach reduces errors and enhances overall product quality. Automation in quality assurance allows for more frequent and consistent checks. This boosts the importance of DPI. It ensures problems are caught earlier, which saves cost and time. The future might see FRI complementing a robust DPI system, rather than acting as the sole quality gatekeeper.
Conclusion: Balancing Cost, Quality, And Efficiency
DPI (During Production Inspection) and FRI (Final Random Inspection) are both critical. Ensuring product quality is a top priority for businesses manufacturing goods. Performing DPI allows for early detection of issues. This helps in minimizing risks and saving costs. Considering both inspections can lead to optimal outcomes. FRI, conducted at the end of production, also plays a vital role. It ensures the overall quality of the batch meets the standards. Employing best practices such as using production checklists, communicating standards clearly, and training inspectors thoroughly is crucial. Such measures maintain consistency and quality in products. Companies must weigh the benefits against the costs. Deciding to perform both DPI and FRI offers greater confidence in product quality. This approach usually leads to customer satisfaction. Ultimately, the choice depends on the company’s quality control strategy and budget allowances.
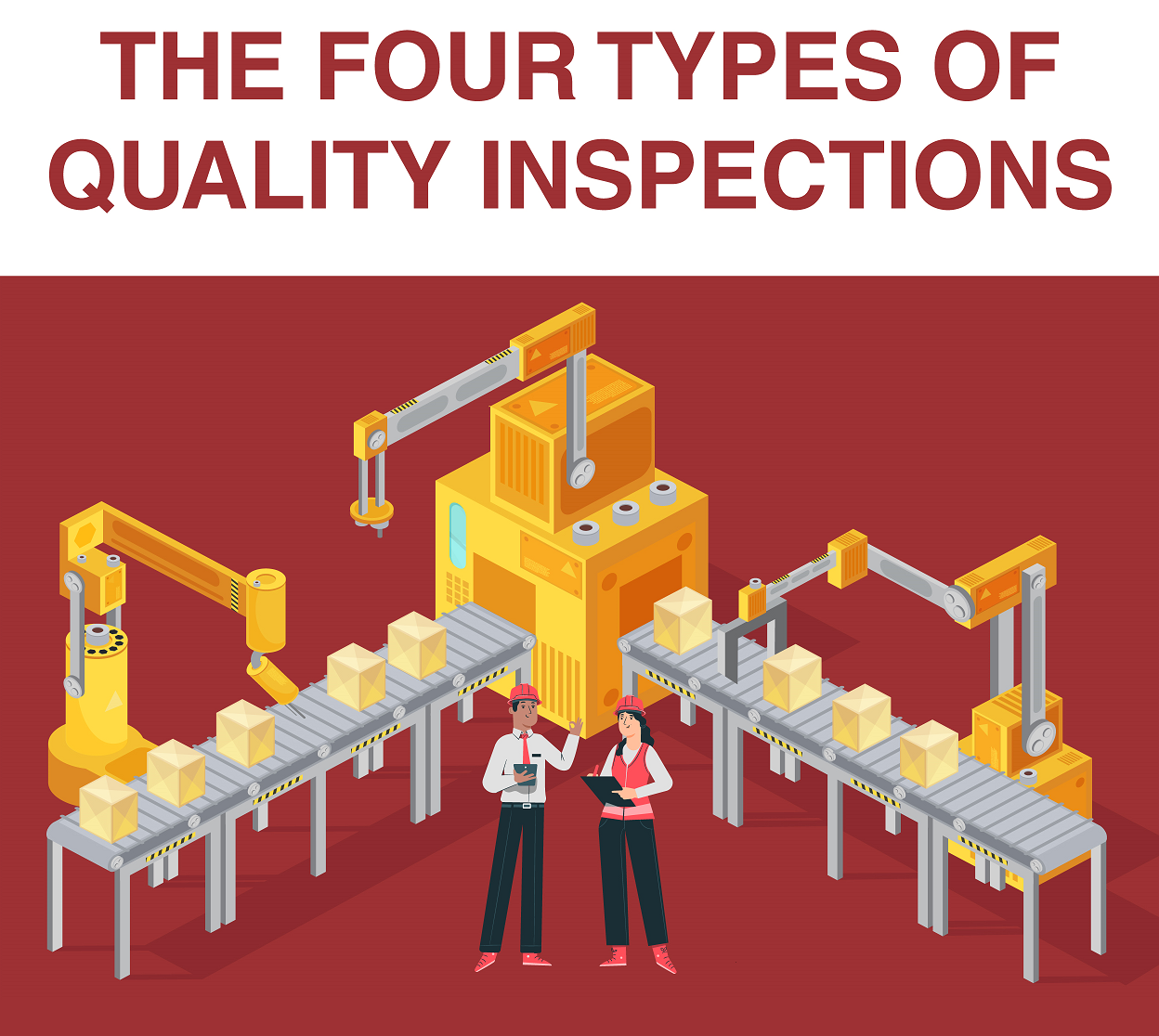
Credit: www.hqts.com
Frequently Asked Questions For Is It Mendatory For Doing Dpi (during Production Inspection) Before Fri (final Random Inspection)
What Is Dpi In Manufacturing?
DPI stands for During Production Inspection. It is a quality control process. Factories apply it when products are about 10-60% manufactured. It helps identify defects early.
How Does Dpi Differ From Fri?
DPI occurs during production, much earlier than FRI. It allows for timely corrections. FRI is the final check before shipment, confirming order completion and standards.
Is Dpi Mandatory Before Fri?
DPI is not mandatory but highly recommended. It ensures quality mid-production. Skipping DPI could risk product defects missed by only conducting FRI.
What Are The Benefits Of Dpi?
DPI provides early defect detection and allows for adjustments. It reduces the risk of non-conformities, helps manage production timelines, and builds confidence in product quality.
Conclusion
To summarize, weighing the need for DPI alongside FRI ensures quality control at multiple production stages. It helps in identifying defects early on, potentially saving time and resources. Implementing both inspections can be seen as a proactive step to assure the end product meets the highest standards, fostering consumer trust and sustaining your brand’s reputation.
Quality-centric businesses would do well to consider both DPI and FRI in their protocols.